The First Triple Certified Facade
Merging sustainability and building well-being
Presented on August 5, 2020 at Facade Tectonics 2024 World Congress
Sign in and Register
Create an Account
Overview
Abstract
Johnson Controls (JCI), a leading provider of intelligent building technology solicited the design of a 35,000sm headquarters for its Asia-Pacific Region in Shanghai. JCI and Gensler set high sustainability goals for the project which has resulted in the first building in China to receive all three top sustainability certifications; USGBC LEED Platinum, China Green Building Design Label Three Star Certification, IFC-World Bank EDGE Certification. A narrow site presented a challenge; how to create a sense of community while optimizing floorplate efficiency. The solution created two rectangular buildings to maximize daylight and views. These buildings were bent in opposite directions, creating a large space in between that serves as a gathering space.
Facade strategies were developed to achieve high levels of energy efficiency resulting in 44% savings. The facade is composed of custom unitized curtain wall panels which incorporate SSG glazing units with high insulation value metal panels at the spandrel condition. This combination increases thermal properties, achieves proper window-to-wall ratios and reduces solar glare. Complex building curves and geometry were addressed with unique panel designs incorporating curved mullion extrusions and custom panel edge profiles. High performing low-E coated low-iron glass units were specified. A high opacity frit pattern was used at insulated shadow boxes to gradient the change from opaque to vision areas. Large scale bi-directional curved GFRC panels were designed to provide a transition band of material mirroring the flow of water from Suzhou Creek.
Building well-being design is itself a sustainable goal and is essential in mega-cities like Shanghai where dense urban environments challenge the way we achieve healthy lifestyles. JCI is investing in human capital by providing their employees with a progressive workplace design that mirrors the goals of their company. Environments that promote social connectivity foster innovation and have a direct benefit on quality of life. The design team chose to focus on three aspects of building well-being design: socially connected spaces, daylight and views, and access to outdoor areas. This presentation will explore how the facade design was an integral part of sustainable and building well-being goals of the project resulting in a new benchmark.
Authors
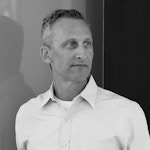
Stephen Katz, AIA, LEED AP BD+C
Senior Associate
Gensler
stephen_katz@gensler.com
Keywords
Introduction
The site for the building is narrow and has a 24m height restriction due to the proximity of Hongqiao Airport. This presented a unique challenge: how to create a sense of community on a linear site while optimizing floorplate efficiency. The solution was to create two long rectangular buildings to maximize daylight and views. These separate buildings were bent in opposite directions and then joined together, creating a large atrium in between that serves as a central community gathering space. Open circulation paths surround the atrium and each floor is linked by staircases to provide a platform for cross community connections, chance interactions and physical activity. Ample research links these types of conversations across departments and business units to increased productivity and innovation.
Along the north side of the site is a large public park. According to city planning requirements, public access through Johnson Controls’ site to this park was mandatory. By lifting the north wing, we were able to create a green public walkway through the site without compromising Johnson Controls’ mandate for a single building. The design solution allowed an expansive outdoor setting for staff, public access to the park and offered employees daily interaction with nature in one of the densest urban centers in the world. A south wing was created to incorporate a Canteen and private courtyard which adds to the variety of onsite amenities and helps build community among employees.


Background
China’s need for new office buildings continues to increase making it the world’s largest construction market. The Chinese government has taken notice and has mandated that almost every new building over 20,000sm meet China Green Building Design Label Certification standards. While these actions are a step in the right direction in efforts to fight climate change, there is an equally important need to integrate building well-being design with energy savings strategies. Progressive approaches to the human experience in building design are essential to fostering productivity and innovation, and China is searching for new ways to elevate its service economy. Centers of manufacturing in China are being replaced by smart cities and this project a case study in combining energy efficiency, building well-being design and progressive uses of technology. The economic shift in China to a service-based economy means an increased importance factor for the design of successful office buildings. The quality of office buildings now means more than the quantity. As in US, European and Japanese markets, the office building in China has become a direct reflection of the values of that company for employees who work there and for customers who tour the building.
As David De Cremer and Jason D. Shaw have noted, “In a service-driven economy, customers cannot be lured in with cheap, low-quality offerings. Now, customers will demand high-quality products, and for that they are willing to pay more. To differentiate your company, it thus becomes necessary to communicate to customers why you are in the business of selling this particular product and what value it brings to the customer” (De Cremer et. al., 2016). This statement is entirely applicable to office building design. Johnson Controls needed a quality building to foster innovation, retain existing employees, attract new talent and let customers know that this is a company which designs and builds with cutting edge technology.

Sustainability
Sustainability is at the core of Johnson Controls’ identity as a company. Their commitment to leveraging technology to solve energy efficiency problems dates to Warren Johnson’s 1883 patent of the first electric room thermostat. Fast forward to 2018 and one finds a company fully invested in smart building technology and with a progressive stance on fighting climate change. Johnson Controls’ new headquarters in Shanghai is the embodiment of their commitment to working in China and the Asian market which will have significant building construction growth for the foreseeable future. A major goal for the design team was to establish a model of sustainable and intelligent building design for the Chinese market. The Headquarters Asia Pacific is the first building in China to receive these three global energy efficiency awards:
- U.S. Green Building Council’s LEED Platinum Certification
- China Green Building Design Label Three Star Certification
- IFC-World Bank Group’s EDGE Certification
In order to achieve LEED Platinum and China Green Building Design Label Three Star and certifications, sustainability was a top project priority and paramount to the design approach. EDGE certification was granted at both the design phase and project completion, and this recognition marks a first for an office building in China. The International Finance Corporation (IFC), a member of the World Bank Group, created the EDGE program as a green building certification system available in more than 100 economies.
Sustainable Systems Summary
Mechanical
- Optimized central plant with centrifugal chillers, centrifugal compressor magnetic drive water cooled chillers, Heat pumps and a water-to-water heat pump.
- Underfloor Air Distribution System (UFAD) with a passive floor mounted chilled beam. This is a rare dual application in China.
- Decoupled mechanical system, radiant heating and cooling in the atrium to maximize occupancy comfort and reduce energy usage, ice storage mechanical system to reduce peak demand cooling loads.
Electrical
- In-building Johnson Controls Distributed Energy Storage Units (scalable battery based).
- 2,000sm of solar panels (PV and solar thermal).
- Intelligent LED lighting system with daylight dimming, occupancy sensors and integrated interior façade roller shade system.
- 750sm atrium skylight with integrated intelligent roller shade system.
- 6 hybrid and electric vehicle charging stations which enable employees to commute with a smaller carbon footprint.
Plumbing
- Rainwater collection system: rainwater is collected from 8000m² of roof area via a syphonic drainage system and stored in a 370m³ storage tank in the basement.
- Grey water system: grey water is collected from showers, hand washing, and HVAC condensate and stored in a 30m³ tank in the basement. The collected water is treated through an automatically controlled filtration system comprised of a normal filter, MBR system and an automatic chlorine dosing control system.
Landscaping
- Green roof system for solar heat gain reduction.
- Low-maintenance site plantings.
Major Sustainability Statistics
- 45.47% in energy savings annually, 42.27% in water savings annually.
- 20.82% less embodied energy using FSC certified wood-based building materials.
- Predicted above grade EUI is 4,276,422 KWH per year over 35,064m² = 121.96KwH/m²/yr excluding on-site renewable energy contribution.
- Predicted above grade EUI is 4,111,422 KWH per year over 35,064m² = 117.25KwH/m²/yr including on-site renewable energy contribution (carbon offsets not counted).
- Energy cost saving compared to ASHRAE standard: 44%.


Methodology
Building Well-being Definition and Design Concepts
Building well-being design can be defined as environments which have “strong positive effects on occupant well-being and functioning, especially attributes such as the amount and quality of light and color, the sense of enclosure, the sense of privacy, access to window views, connection to nature, sensory variety, and personal control over environmental conditions” (WBDG Productive Committee, 2016). Building well-being design is itself a sustainable goal and is essential in mega-cities like Shanghai, where dense urban environments challenge the way we work and achieve healthy lifestyles. Johnson Controls is investing in human capital by providing their employees with a progressive workplace design that mirrors the goals of their company. Environments that promote social connectivity foster innovation and have a direct benefit on quality of life.
The design team focused on three aspects of building well-being design each of which has implications for the shape of the building in addition to performative values; daylight and views, access to usable outdoor areas, socially connected spaces.
Daylight and Views
The long rectangular shaped floor plates created an opportunity to provide access to natural light and views to landscaped exteriors. Workstations and collaboration areas are in close proximity to windows. In addition to reducing the amount of energy used for artificial lighting, this exposure to natural light offers psychological benefits during the workday as well as quality-of-life improvements such as sleep (Mohamed et. al., 2014). Views out of the building were important to the design team. Surrounding the building with green landscaping reduces urban heat island affects but also provides an opportunity for visual connections with nature which are critical in intense urban environments.
Access to Usable Outdoor Space
Distributing accessible and usable outdoor space throughout the building both at ground level and above gives employees choice in where they work—focus areas, places for collaboration, and options for a change of scenery—not to mention the connection to green space many residents of large cities often lack. Each floor has a terraced balcony where people can work outdoors or take a break. These build to a large two-level outdoor roof deck where casual gatherings or formal group meetings can occur. At the ground level, an outdoor Canteen courtyard off the dining area connects to a park along adjacent Suzhou Creek. This outdoor retreat includes a water feature and is visually linked to the terraced balconies. The sum of these areas is a network of distributed, usable and flexible outdoor spaces which serves as a productivity and well-being catalyst.
Socially Connected Spaces
The design team chose to create a five-story central atrium space to join the two rectilinear office bars. This move presented an opportunity provide an indoor area not only for large all-hands gatherings but since each floor is linked around the atrium with staircases, frequent interactions and casual “collisions” are more likely. The idea is to promote conversations across departments and business units within the company. Numerous studies indicate that office environment productivity increases when chance encounters increase. The open circulation paths around the atrium at this building provide a platform for cross community connections and promote physical activity during the workday. The intended result is innovation, an essential tool for an engineering environment.
Data and Explanation
Facade System Goals and Strategies
There were several important considerations for the design of the façade systems; the need for high thermal performance due to intense sustainability and energy modelling goals, adaptability to complex geometries with multi-directional curved and angled surfaces, the ability to accommodate numerous transitions to outdoor spaces (including balconies, terraces, roof decks), the ability to handle the atrium long span structural system cladding needs, a focus on façade border conditions to achieve a tightly sealed building envelope. While the building has eight façade systems, this paper will focus on three systems which were able to achieve a critical balance between sustainable performance, enhancing building well-being and design form and shape.
Facade System 1 (FS-1) Unitized Curtain Wall
The major unitized curtainwall system is designated as Façade System 1 (FS-1) and is composed of custom extruded thermally broken aluminum mullions. The double insulated glass units (DIGUs) are captured at the top and bottom and utilize structural silicone glazing (SSG) connections at the vertical panel to panel joints. Aluminum edge profiles at each vertical panel to panel joint provide sharp, clean terminations. The typical module is 1.5m by 4.4m. The FS-1 spandrel condition is rather tall at 1.5m owing to a raised access floor system and upturned concrete beam at the perimeter.
Each typical FS-1 panel has three parts:
- A 1500mm tall vented 3mm thick plate aluminum panel at the top. Behind the aluminum panel is an air space and a 90mm thick aluminum insulated back pan.
- A 700mm tall code required electronically controlled smoke exhaust window is in the middle. The smoke exhaust window has a vision glass DIGU with an air space and insulated shadow box behind it. The window glass is fritted with a white high opacity dot pattern which serves as a gradual visual transition from the white metal panel above to the non-fritted vision unit below.
- A 2200mm tall vision unit at the bottom. Grey silicone sealant and gaskets were used exclusively on the project for all façade systems.
The FS-1 vision glass is SYP (Shanghai Yaohua Pilkington) low iron substrates with a laminated outer light. The low-E coating is YKE0660 which yields a Visible Light Transmittance of 51%, a U-Value of 1.3 W/m2K, a Shading Coefficient of .35 and an Exterior Reflective Value of 11%. This coating was specifically chosen for the balance between visible light and energy performance. Furthermore, the code required exterior glare study mandated a maximum of 11% reflectivity due to nearby residential buildings. The Heat Transfer Coefficient U-Value of the whole curtainwall system for FS-1 is 1.817 W/m2K which is a 73% performance increase over code requirements. One of the most important façade design factors for this project was the window-to-wall ratio (WWR). Many award-winning office buildings feature WWRs exceeding 70% which result in substantial HVAC loads. The design team recognized the advantage of lowering the WWR and chose a high quality, well insulated spandrel metal panel solution.
Curved geometries feature prominently throughout the design of this project. The flow of water from adjacent Suzhou Creek is mirrored onto the building at corners and façade border conditions. This meant achieving 3m to 2.3m radius outside and inside curved unitized curtainwall panels with curved DIGUs and metal panels. There are no segmented façade applications.


Facade System 2 (FS-2) Stick Fabricated Curtain Wall with GFRC Soffit
The majority grade level condition is designated as Façade System 2 (FS-2) and is composed of custom extruded stick fabricated thermally broken aluminum mullions. The double insulated glass units (DIGUs) are captured at the top and bottom and utilize structural silicone glazing (SSG) connections at the vertical joints. The typical module is 1.5m by 5.9m. At the top of the glazed area is a 650mm high code required electronically controlled smoke exhaust window. This exhaust window has a vision glass DIGU with an air space and insulated shadow box behind it. The vision glass below the exhaust window matches that of FS-1.
The uppermost portion of FS-2 is a custom Glass Fiber Reinforced Concrete (GFRC) panel system. The GFRC panels are 15mm thick and are designed to act as a rain screen. A continuous water/air/vapor-proof membrane and substrate exists behind each GFRC panel. An air space separates the back of the GFRC panel from the membrane. The design team chose GFRC as the material to serve as the transition zone from the upper level unitized curtainwall panels to the grade level stick fabricated system for several reasons. Because GFRC can be cast into complex geometric forms, this material is able to accommodate the desired shape of the panels. This vertical wall element is set at bi-directional angles that then shifts and morphs to an overhead horizontal angled soffit condition. The complex geometry of this feature was modelled using Rhinoceros software and transferred to Revit for final documentation.
Of critical importance to the design team was the final visual size of the GFRC panels. From a design standpoint, it was desired to have no panel joints parallel to the outer edge of the angled wall or the inner edge where it meets the ceiling and window system. This would have resulted in panels sizes of 3m by 5m which would likely result in GFRC panel cracking due to thermal and building movements. The solution involved working with the GFRC manufacturer to provide multiple smaller panels that were joined together post installation on site with a high elastic mortar backed by a high strength mesh fabric which is then bonded to the GFRC panels with epoxy. A coloured protective coating is then applied on site over all panels presenting a unified surface.


Another important aspect of the panel design involved the connection details. The GFRC panels have hidden steel angle connections on the back side which are then secured to tube steel framing members located behind the weather barrier and substrate. Each side of the panel joints have steel angle connections which means that the individual panels are restrained from moving. The high elastic mortar joint takes up panel thermal movement. This system took a substantial amount of investigation including full size mock-ups, but the result created a fluid surface which met the design team’s goal.
The GFRC panels provide a unique textured surface especially at night. This more varied surface serves as a contrast to the smooth surfaces of the glass and aluminium panels. A narrow light fixture trough was integrated at the inner edge creating a dramatic night time effect. Separating the GFRC panels from the window system is a continuous 150mm high by 96mm deep aluminium channel. These small but well-crafted details are important outer edge terminations for the GFRC system.
Facade System 4 (FS-4) Terraced Balcony Assemblies
One of the major building well-being goals for this project involved creating a distributed network of usable outdoor spaces. These are places where people can work outdoors or simply find a place to take a break. Locating numerous outdoor terraced balconies across the building at every floor level had several detailing implications for the façade. The cast-in-place concrete structural members were sloped 30 degrees in order to permit daylight to enter the floor which complicated efforts to achieve a uniform high performing building envelope.
The major façade detailing challenges for FS-4 involved maintaining a continuous layer of insulation and waterproofing. This was difficult as the insulation and waterproofing materials require numerous transitions first from the window head, then to a GFRC clad soffit, then below a glass guardrail to a roof system located below open jointed stone pavers on pedestals with final termination to the sill of the window and door systems. Careful attention was paid to waterproofing and insulation material compatibility which was reviewed with the Contractor at pre-installation conferences and during construction phase field observation meetings.
The GFRC clad soffit features complex geometry with angled surfaces facing skyward and downward at 20-degree angles. A redundant waterproofing system was employed for the soffit with a continuous water/air/vapor-proof membrane (composed of a self-adhered rubberized asphalt sheet material) and substrate behind the GFRC panels and a continuous fluid applied waterproof membrane applied to the portions of the cast-in-place concrete slab extending beyond the window system. Both waterproofing systems marry up to the roofing waterproof systems inboard of the glass guardrail. While in United States markets, one would typically utilize fiberglass mat gypsum sheathing, the local construction preference was cement board sheathing.
Incorporating balconies and terraces is a wonderful way to integrate building well-being design features. Additional care is required with respect to maintaining high levels of building envelope performance and reducing maintenance costs. Water and thermal bridging management are two key areas. The benefits of usable outdoor space for building occupants are significant so it is important to treat the design of outdoor spaces with a high level of consideration.


Conclusion and Future Work
In order to understand the details and components of a building’s façade, one must first step back and appreciate the larger context which drives decisions for performance values, material selection and design compatibility. For the Johnson Controls Headquarters Asia Pacific this started with the market context in China which is balancing construction sector growth and a recognition of the importance of high quality building design. Attention is being paid to office environments which promote notions of building well-being such as access to daylight, usable outdoor space and creating socially connected spaces. The results can be dramatic for employee productivity, innovation, decreased sick days and the ability to attract top level talent. The implications for façade design require increased attention to daylighting strategies, how to approach façade spandrel conditions, effective border condition transitions and great care when detailing outdoor spaces. One should not lose sight of sustainable building goals and how the building envelope needs to be a part of the overall energy use performance narrative. Many sustainable project metric results become the outward public face of the building in terms of sustainable ratings, tracking facility costs and returns on investment. The façade system strategy for this project benefited from a continued effort to simplify details when possible to increase the chance of successful implementation.
Acknowledgements
The author wishes to thank the following people for their insights and support:
Ward Komorowski, Johnson Controls
Brian Pfeifer, Johnson Controls
Ann Stark, Johnson Controls
Benjy Ward, Gensler
Steve Meier, Gensler
Xiaomei Lee, Gensler
Peter Weingarten, Gensler
Edward Chao, Gensler
Eric Gannon, Gensler
Willie Wai, Gensler
Ellie Wang, Gensler
Debrah Vander Heiden
Zia Tyebjee
Rights and Permissions
De Cremer, David and Jason Shaw. “What China’s Shift to a Service Economy Means for Its Managers.” Harvard Business Review(2016).
WBDG Productive Committee, US National Institute of Building Sciences. “Promote Health and Well-Being”, Whole Building Design Guide (2016).
Boubekri, Mohamed, Ivy Cheung, Kathryn Reid, Nai-Wen Kuo, Chia-Hue Wang and Phyllis Zee. “Impact of Windows and Daylight Exposure on Overall Health and Sleep Quality of Office Workers: A Case-Control Pilot Study.” Journal of Clinical Sleep Medicine (2014).