Hydroformed Shading
A Calibrated Approach to Solar Control
Presented on August 12, 2020 at Facade Tectonics 2024 World Congress
Sign in and Register
Create an Account
Overview
Abstract
New approaches to lightweight metal forming have the potential to advance architectural fabrication, particularly in the design and engineering of high-performance building envelopes. For the Harvard Science and Engineering Complex outside Boston, Behnisch Architekten, together with Knippers Helbig, applied a novel application of metal shaped by water in the world’s first hydroformed tensile facade system.
Hydroforming is an industrial cold forming process in which a metal blank is driven into a single mold with hydraulic pressure to form extremely thin parts with exceptional structural stiffness. It has been developed and advanced primarily by the automotive and aerospace industries—where weight to strength ratio has a compound effect on production cost, safety, performance, and energy consumption. Despite parallel considerations, it has not been widely used in architectural applications.
The Harvard screen facade was developed through a rigorous research process to apply hydroforming in a sun shading system that leverages the advantages of this technology, namely lower tooling costs, precise geometric definition, and superior structural properties. Calibrated to the extreme seasonal variations of the New England climate, the system is optimized to temper solar heat gain in the summer while maximizing daylight and solar energy in the winter. The screen is comprised of a series of 12,800 hydroformed panels of 1.5 mm thick (16 gauge) stainless steel, measuring 2.5 x 2.5 ft, each weighing under 10 pounds. The panels are supported by an ultra-lightweight tensile structure with a cross sectional area of just 0.35 in2. Despite its delicate appearance, the shading screen is a crucial component in the comprehensive energy strategy of the new academic building, which opens in 2020.
Authors
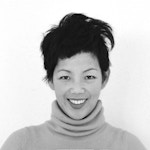
Michelle Siu-Ching Lee
Architect
Behnish Architekten
research@behnisch.com
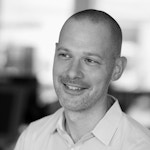
Robert Matthew Noblett
Partner
Behnish Architekten
rmn@behnisch.com
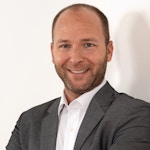
Roman Schieber
Associate Director
Knippers Helbig GmbH
R.Schieber@knippershelbig.com
Keywords
Introduction
At 535,000 sf, the Harvard Science and Engineering Complex (SEC) unifies and expands multiple science and engineering disciplines in a new centralized location in Allston, Massachusetts. As the primary home
Access Restricted
Background
The sun shading system for the Harvard SEC emerges from the synthesis of three topics that have been widely researched employed in architecture, engineering and manufacturing but rarely combined simultaneously
Access Restricted
Methods and Data
Screen Performance Testing
Because of the uniqueness of the design, several specialized full-scale tests were conducted to validate assumptions and test unknowns.
Dynamic Test
During design and engineering of the external screen, the
Access Restricted
Construction and Maintenance
The screen panels and the tensile components are engineered and fabricated in Germany, and shipped to the site and installed by Permasteelisa North America under Turner Construction. The off-cuts from
Access Restricted
Conclusion
The sun shading screen of Harvard University’s Science and Engineering Complex demonstrates the unique potential of hydroforming technology to create high performance, lightweight, and structurally stiff components. The ability of
Access Restricted
Acknowledgements
Behnisch Architekten: Stefan Behnisch, Michael Cook, Magdalena Czolnowska, Daniel Mazur
Knippers Helbig: Nicola Haberbosch
Josef Gartner: Klaus Reuschle, Reiner Haselmeier, Günter Muller
Edelstahl Mechanik: Philipp Eisele
Transsolar: Linda Lam, Erik Olsen
Turner Construction: James Riley, Tiago Pimentel
Harvard University: Alyssa Hubbard, Joe O'Farrell
Rights and Permissions
References
Barber, Daniel. “The Form and Climate Research Group, or Scales of Architectural History.” In Climates: Architecture and the Planetary Imaginaryedited by James Graham, Lars Muller Publishers, 2019.
Bell, Colin, Caleb Dixon, Bob Blood, Jonathan Corney, David Savings, Ellen Jump, Nicola Zuelli. “Enabling sheet hydroforming to produce smaller radii on aerospace nickel alloys.” International Journal of Material Forming. September 2019, Volume 12, Issue 5, pp 761–776
Bell, C, Jonathan Corney, David Savings, John Storr. “Assessing the potential benefits of manufacturing gas turbine components by utilizing hydroforming technology.” 13th International Cold Forming Congress; 2nd - 4th September 2015, Glasgow.
Braham, William. "Biotechniques: Remarks on the Intensity of Conditioning" in Kolarevic, Branko, Ali Malkawi, ed. Performative Architecture: Beyond Instrumentality. Spon Press, 2005.
Bundesministerium des Innern, für Bau und Heimat (German building material database for assessment of global ecological effects). https://www.oekobaudat.de/(accessed March 25, 2019).
Kang, Beom-Soo , Bo-M Son, Jeong Kim. International Journal of Machine Tools and Manufacture
Volume 44, Issue 1, January 2004, Pages 87-94.
Grynning, Steinar, Berit Time, Barbara Matusiak. “Solar shading control strategies in cold climates-Heating, cooling, demand and daylight availability in office spaces.” Solar Energy, September 2014, Vol.107 (2014): 182-194.
Houska, Catherine. “Facades: The Use of Stainless Steel in Second-Skin Facades.” Council on Tall Buildings and Urban Habitat. Journal Issue III, 2013.
Olygyay, Victor. Design with Climate: Bioclimatic Approach to Architectural Regionalism. Princeton University Press, 1963.
Schlaich, Jorg, Rudolph Bergermann. Light Structures. Prestel, 2004.
Subhashchandra, Pandya Rajen, Bahr Behnam. "Prediction of Variation in Dimensional Tolerance Due to Sheet Metal Hydroforming using Finite Element Analysis." Journal of Aerospace (2006): 563-567.
Zheng, Kailun, Denis J.Politis, Liliang Wang, Jianguo Lin. “A review on forming techniques for manufacturing lightweight complex—shaped aluminium panel components.” International Journal of Lightweight Materials and Manufacture. Volume 1, Issue 2, June (2018):55-80.
Photos by Janis Roykalns, Roman Schieber, and Christopher Karlson.