Evaluating Additive Manufacturing for Metallic Facade Components
Sign in and Register
Create an Account
Overview
Abstract
The state-of-the-art of Additive Manufacturing (AM), popularly known as 3D printing, shows its prospective future in the Architecture-Engineering-Construction (AEC) industry, side-by-side with the conventional manufacturing (CM). AM building components are likely to have higher energy efficiency and environmental sustainability than the CM counterparts. However, currently AEC practitioners do not consider AM’s application in their projects because they are not informed about AM’s characteristics compared to CM in a rapid and consistent manner required for AEC projects. If AEC practitioners had systematic means to rapidly and consistently evaluate the choice between AM and CM for producing building components through transparent criteria such as cost and environmental impacts, they could make well-informed decisions about utilizing AM in their projects.
Firstly, well-documented comparative analyses of AM vs. CM for producing two metallic curtainwall components were carried out in collaboration with a global curtainwall contractor. These case studies included Life Cycle Assessment (LCA), cost and schedule analyses and demonstrated that AM for metallic curtainwall components is technologically feasible and can lower environmental impacts by up to 87%, but is cost-prohibitive today. Secondly, based on the case studies, a 7-activity assessment framework was developed that allows AEC practitioners a systematic way to assess the applicability (A), schedule (S), environmental impacts (E), and cost (C) of AM vs. CM to produce building components.
Finally, introduced in this paper, the application of this semi-automated framework showed that it speeds up the assessment of all four ASEC analyses for more than 22 times, and makes them more consistent. However, the consistency analysis of the ASEC results demonstrated that the inconsistencies of the E results are further expected due to current uncertainty sources related to human factors and LCA tools, having greater impact on the assessment than the framework. Furthermore, regular updates of the framework’s databases are required to maintain the consistency of the A, S and C results.
The use of the formalized framework showed the superiority of the speed and the consistency of the AM vs. CM assessment over the assessment without the framework for specific metallic facade components. With the framework AEC practitioners could make well-informed decisions about utilizing AM in their projects in a timely and consistent manner. Future work includes fuller automation of the framework and testing its generality on building components in various material types other than metals.
Authors
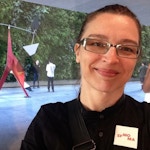
Natasa Mrazovic, M. Arch. Eng., M.C.E.
Stanford University
natasam@stanford.edu
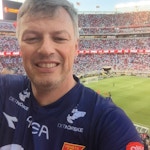
Martin Fischer
Stanford University
fischer@stanford.edu
Keywords
Introduction
Four years ago, the hype around Additive Manufacturing (AM) technologies, popularly known as 3D printing, brought attention to the features and benefits these technologies are providing to other industries, like
Access Restricted
Background
To assess the potential worth of the research and determine the availability of data, the authors first developed and conducted the case studies, and then formalized an assessment framework based
Access Restricted
Validation of the Formalized Framework
To understand and quantify the value of the formalized framework presented above, the impact of this semi-automated framework on the effort required for the ASEC analyses was assessed. The speed
Access Restricted
Validation Results - Speed of the Assessment
The analysis of the time required for each assessment step showed that the use of the formalized framework speeds up the assessment by 97.1% in total per case for the
Access Restricted
Validation Results - Consistency of the Assessment Results
The formal, partially automated application of the framework improves the consistency of results for all four ASEC analyses. The use of the framework produced identical A, S and C results
Access Restricted
Conclusion and Future Work
The foreseeable future brings the application of AM technologies to the AEC industry. The case studies of AM building components showed AM’s potential to reduce the environmental impacts over CM
Access Restricted
Acknowledgements
This research was conducted with the support of Stanford University, Center of Integrated Facility Engineering (CIFE) at Stanford, and with the support and in collaboration with the Permasteelisa’s R&D Group.
Rights and Permissions
Additive Manufacturing Research Group, Loughborough University, Atkins Technology Strategy Board, Alcon, Bentley, Boeing, Delphi, Econolyst, Renishaw, and Virgin Atlantic. 2012. “Atkins Project: Additive Manufacturing; A Low Carbon Footprint.”
Arnstein, Joe, Brittany Gibbons, Amir Hashemi, Jordan Pratt, and Paul Zhu. 2015. “Consequential Life Cycle Assessment of Conventionally Manufactured and 3D-Printed Curtain Wall Brackets.” Stanford: Stanford University.
Baker, Jack W., and Michael D. Lepech. 2009. “Treatment of Uncertainty in Life Cycle Assessment.” In . Boca Raton: CRC Press.
Baumers, Martin. 2012. “Economic Aspects of Additive Manufacturing: Benefits, Costs and Energy Consumption.” Loughborough University, UK. https://dspace.lboro.ac.uk/dspace-jspui/bitstream/2134/10768/3/Thesis-2012-Baumers.pdf.
Clayton, Mark, John Kunz, and Martin Fischer. 1998. “The Charrette Test Method.” CIFE Technical Report #120. Stanford University.
Fong, Curtis, Cesar Marco, Shiran Shen, and Mark Soendjojo. 2016. “Life-Cycle Analysis of Additively Manufactured vs. Conventionally Manufactured Aluminium Curtain Wall Frames.” Stanford University.
Gandini, Alejandro, Christina Logan, David Tse, Giuliana Galante, and Ryan Coakley. 2015. “Aluminum Facade Frame: Conventional vs. Additive Manufacturing.” Stanford: Stanford University.
Gao, Weixuan, Michelle Gu, Wanning Lyu, Amanda Piao, Bochen Zhang, and Shuyi Yin. 2016. “Life Cycle Analysis of Additive Manufacturing vs. Conventional Manufacturing for Curtain Wall Bracket.” Stanford University.
Gibson, Ian, David W. Rosen, and Brent Stucker. 2010. Additive Manufacturing Technologies Rapid Prototyping to Direct Digital Manufacturing. Springer US. http://link.springer.com/book/10.1007%2F978-1-4419-1120-9.
Heijungs, R., and M. a. J. Huijbregts. 2004. “A Review of Approaches to Treat Uncertainty in LCA.” 339. http://repository.ubn.ru.nl/ha... 14040:2006. n.d. “ISO 14040:2006 - Environmental Management -- Life Cycle Assessment -- Principles and Framework.” Accessed February 22, 2016. http://www.iso.org/iso/catalogue_detail?csnumber=37456.
Khoshnevis, Behrokh. 2004. “Automated Construction by Contour Crafting – Related Robotics and Information Technologies.” Journal of Automation in Construction – Special Issue, January.
Lacirignola, Martino, Philippe Blanc, Robin Girard, Paula Pérez-López, and Isabelle Blanc. 2017. “LCA of Emerging Technologies: Addressing High Uncertainty on Inputs’ Variability When Performing Global Sensitivity Analysis.” Science of The Total Environment 578 (February):268–80. https://doi.org/10.1016/j.scitotenv.2016.10.066.
Mrazovic, Natasa. 2014. “State of the Art of 3D Printing/Additive Manufacturing Technologies and Their Possible Future Application in the Construction Industry.” presented at the 78th EUROCONSTRUCT® Conference, Milano, Italy, November 19. http://www.euroconstruct.org/publications/publications.php.
Mrazovic, Natasa. 2015b. “Feasibility Study to 3D Print a Full Scale Curtain Wall Frame as a Single Element (Application of 3D Printing/ Additive Manufacturing Technologies in the AEC Industry).”
Mrazovic, Natasa. 2015a. “A Framework for Bringing 3D Printing into the Construction Industry | Center for Integrated Facility Engineering.” Stanford University. http://cife.stanford.edu/Frameworkfor3DPrinting.
Mrazovic, Natasa, Martin Baumers, Richard Hague, and Martin Fischer. 2017. “Guiding Building Professionals in Selecting Additive Manufacturing Technologies to Produce Building Components.” The Elsevier 3D Printing Grand Challenge - Materials Today Communications Journal. manuscript in review.
Mrazovic, Natasa, Danijel Mocibob, Michael D. Lepech, and Martin Fischer. 2017. “Assessment of Additive and Conventional Manufacturing: Case Studies from the AEC Industry.” In Proceedings ISEC PRESS. Valencia Spain. https://www.isec-society.org/ISEC_PRESS/ISEC_09/html/Su-15.xml, DOI: 10.14455/ISEC.res.2017.201.
Ruffo, M., C. Tuck, and R. Hague. 2006. “Cost Estimation for Rapid Manufacturing - Laser Sintering Production for Low to Medium Volumes.” Proceedings of the Institution of Mechanical Engineers, Part B: Journal of Engineering Manufacture 220 (9):1417–27. https://doi.org/10.1243/09544054JEM517.
Sedjo, Roger A. 2013. “Comparative Life Cycle Assessments: Carbon Neutrality and Wood Biomass Energy.” SSRN Scholarly Paper ID 2286237. Rochester, NY: Social Science Research Network. https://papers.ssrn.com/abstract=2286237.
Strauss, Holger. 2013. “AM Envelope. The Potential of Additive Manufacturing for Facade Constructions.” A BE | Architecture and the Built Environment 3 (1):1–270. https://doi.org/10.7480/abe.2013.1.
Stucker, Brent. 2012. “Additive Manufacturing Technologies: Technology Introduction and Business Implications.” FRONTIERS OF ENGINEERING Reports on Leading-Edge Engineering from the 2011 Symposium. Washington, D.C.: NATIONAL ACADEMY OF ENGINEERING OF THE NATIONAL ACADEMIES. http://www.nap.edu/openbook.php?record_id=13274&page=ix#s4.
Thunnissen, Daniel P. 2003. “Uncertainty Classification for the Design and Development of Complex Systems.” In Proceedings of the 3 Rd Annual Predictive Methods Conference, Veros Software.
Wang, Annie, and Zach Simkin. 2015. “Rapid Prototyping & Tooling - Senvol_2015-Wohlers-Report.”
COPYRIGHT
All figures are developed by the author. Some small specific individual images in Figures 1, 3 and 4 are sourced online and/or given permission by their owners.