Curved Forming Panel Facades
Origami Folding for Enhancing Diaphragm Strength
Sign in and Register
Create an Account
Overview
Abstract
The performative and visual aspects of curved forming/bending thin “formable” planar materials is explored. Early tests for deflection indicate that curved forming of the surface creates both a decorative and stiffer sheet.
Currently job shop manufacturing techniques typically limit the forming of planar materials to straight lines (press brake forming). Curved shapes are generally associated with more expensive hard tooling. This hard tooling unfortunately also limits variation (cost and time) in components (as compared with more flexible shop tools) especially with more popular parametric variations in facade design. New methods of machining and cutting metals with high performance CNC machining techniques (laser, plasma and water jet) allow for mass customization of panels for rainscreen facades and solar gain control devices with curved features while allowing use of conventional shop tools and CNC techniques.
Panel deflection of rectilinear panelized systems with curved deformed/stiffened features where tested to simulate wind loads. Panel deflection of curved formed surfaces and panels compare favorably with flat reference sheets and panels. Various curved designs are fabricated and tested. The methods and issues of fabricating are evaluated to better understand the effects of curved forming as a viable method of stiffening panels when compared to conventional flat panels.
While curved forming offers the ability to stiffen panels it is also important to improve panels in a decorative way by allowing the flexibility to craft custom designs based on parametric tools and potentially more organic and interesting shapes. Photographs of the samples are included for this visual reference.
The history of curved forming metal and current relevant digital development tools are identified and used to illustrate potential variations on concepts.
The performance of static lighter weight mechanically stiffened rain screen panels can be expanded to include curved formed panels with an integral hinge allowing for dynamic/articulating facades components expanding curved forming to active applications including solar screening and natural ventilation.
Authors
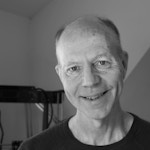
Roger Schroeder
Consultant/Lecturer
Alfred State College
rogerschroeder@icloud.com
Keywords
Introduction
Exterior cladding is a critical element in the appearance and performance of the building as a system. Many materials compete on the exterior for performance with metal composite panels a
Access Restricted
Background
Increasing use of rainscreen facade typologies has increased the interest in panel systems. The demands of rainscreen designs have placed new requirements on some of the functional aspects of panel
Access Restricted
Method
Deflection testing is a critical criteria of facade panel structure, indicating their performance to wind loading. In order to evaluate structural deflection performance, a test fixture and method of loading
Access Restricted
Method- Curved Forming and the Developable Surface
The conventional “straight bend” break forming of panels creates stiffened three-dimensional panels with planar surfaces. Conversely, curved line bending of panels results in curved conical surfaces. For sheet material this
Access Restricted
Data
The samples were evaluated in two forms: 1) without panel returns (no edge flanges forming the panel pan shape), 2) with panel returns (edge returns to create a conventional panel
Access Restricted
Explanation
Deflection Tests (no returns)
The chart Panel Deflection (unreturned edges) (Fig. 9), indicates the significant impact of any curved forming on increasing stiffness (red, blue and yellow) when compared to an
Access Restricted
Conclusion and Future Work
Curved forming creates stiffer panels with the effects varying greatly based on design. Curved shapes in the field of the panel (especially multiple curves) do not assure a stiffer panel
Access Restricted
Acknowledgements
Rigidized Metals Inc. Buffalo, NY provided design expertise and the laser cut stainless steel panels for the evaluation. Gregory Epps, founder of RoboFold was an inspiration to further exploring curved forming.
Rights and Permissions
Kirkpatrick, David D., Danny Hakim, and James Glanz. “Why Grenfell Tower Burned: Regulators Put Cost Before Safety.” New York Times (2017).
“Oil Canning in Metal Roof and Wall Systems.” www.metalconstruction.org/down... (accessed December 1, 2017).
Kolarevic,Branko. Kevin Klinger. Manufacturing Material Effects: Rethinking Design and Making in Architecture. Routledge, 2008.
“Metal Fabrication.” http://www.milgo-bufkin.com/ (accessed August 20, 2017).
“Robofold.” http://www.robofold.com (accessed May 1, 2017).
“Lalvani Studio.” http://lalvanistudio.com/archi... (accessed June 1, 2017).
Ambrose, Tripeny. Building Structures. John Wiley & Sons, 2012.