Connections – Tolerance, Adjustability, Geometric Accuracy
Leveraging Physical Validation with Digital and Iterative Design
Presented on August 26, 2020 at Facade Tectonics 2024 World Congress
Sign in and Register
Create an Account
Overview
Abstract
Connections, those transitions between systems and materials, are critically important when the surfaces are curved or complex. Well-designed connections considered digitally and validated physically, reduced risk, and become precedents for future projects. Gain an understanding of the collaborative and iterative processes used to design connections for two geometrically complex projects.
The complex facade to roof interface at the University of Maryland College Park Brendan Iribe Center for Computer Science and Engineering provides one example of digital practice optimizing and informing geometric design for critical connections. The building’s undulating curved roof edge and the continuous recessed gutter system were unique at every interval. The connection between the facade and the standing seam metal roof required an iterative process using a script to identify the optimum geometry of the roof to wall connection at regular intervals. With this information, the installation team was able to decide between a stick built or a pre-assembled truss solution.
At the United States Olympic Museum, the project team faced a curved and twisted facade with rounded transitions from one plane to the next. Through a facade subsystem design assist, adjustments were made to the primary steel design before fabrication. The structural steel changes provided greater tolerance and more room to operate in the cavity space between the structure and the finished diamond panel skin. Next, the challenge was to cleverly fasten the cold-formed metal framing subsystem to the structural tube steel with sufficient tolerance and adjustability for rapid installation. Critical connection details emerged out of the physical mock-up exercise.
Join the discussion to learn about incorporating tolerance, adjustability, and geometric accuracy into connections between primary structure and the facade, for geometrically complex projects - where it is critical and where it is not.
Authors
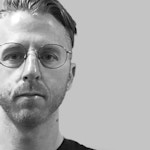
Jeff Montague, RA
Vice President
Radius Track
jeff@radiustrack.com
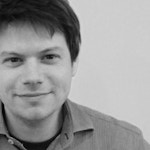
Scott Abukoff
Vice President
Radius Track
Scott@radiustrack.com
Introduction
Turning the corner or more generally articulating how surfaces meet at an edge whether vertical or horizontal is an unavoidable condition in design but has been an obstinate problem in architectural detailing. Defining these conditions as a problem in and of itself is a problem. They are not a problem; they are concepts that one could argue, require additional consideration and discussion regarding how they are to perform as a system.
Recent shifts in architectural design thinking over the last three decades have led to the design of geometrically complex buildings that push the limits of how surfaces meet independently of orientation. Solving these conditions must at a minimum satisfy the increasing demand of building codes that rely on traditional definitions of the facade, roof, and ceiling to define requirements of each system. In addition to these constraints, the advancement of façade surface materials, especially metal, has afforded architects the ability to design architectural systems with infinite variability and minimal tolerances.
This paper presents two case studies where surfaces meet in challenging ways. Each project outlines a systematic approach to the design development, prefabrication, panelization, and installation of exterior subframe systems that support geometrically complex surfaces (facades, roofs, ceilings) (Fig. 1)

A systematic approach is defined as a process where constructability knowledge, custom software tools and workflows, direct fabrication, custom CNC machines, and advanced installation procedures are utilized in a series of feedback loops that encourage an iterative design process where the 3D model and associated database are used during the entire process.
This approach offers the potential to resolve conditions where standard details do not apply and where variability with the architectural surface and transition to adjacent surfaces demands a robust assembly that can anticipate tolerance, account for adjustability, and maintain geometric accuracy.
Explanation
Antonov Auditorium, Univ. of Maryland – Integration of Doubly Curved Concealed Roof Gutter to Singly Curved Façade
From the outset, a successful solution to the development of the roof and façade
Access Restricted
Conclusion
To successfully turn the corner in architecture will continue to challenge how the AEC industry conceptualizes, designs, and constructs buildings. The systems integration effort within both projects described in this paper resolve challenging connections between adjacent surfaces by prioritizing the use of a singular 3D model during the coordination effort to achieve the primary goals of the virtual design to fabrication process (VDC) used across common BIM workflows. With the addition of direct fabrication and advanced installation procedures to the process, the systematic approach to the design to fabrication and installation process promotes the usefulness of the 3D model in downstream processes beyond the completion of the design model or trade contractor shop drawing submission. As a mechanism for communication, the approach allowed key stakeholders within each project to address the nuances of adjustability, tolerance fluctuations and system performance with a commitment to accuracy via quality control checks during system development, fabrication, and installation of each project.
The increased complexity in geometric, performative, and code-based requirements will continue to drive architecture moving forward. A systematic approach to the virtual design to fabrication and installation approach to making buildings within a relational database environment provides a baseline for continued advancement using new materials, technologies, and workflows. Prioritizing constructability expertise and the ability to embed material behavior from physical mockups into the approach affords the process the ability to be both a physical investigation and a digital workflow at the same time.
Rights and Permissions
Antonov Auditorium, The Brendan Iribe Center for Computer Science and Engineering, University of Maryland College Park
Architects: HDR Inc.
Architect of Record: HDR
General Contractor: Whiting-Turner
Roofing & Framing Contractor: JP Construction
Facade Contractor: CHU Contracting
Cold-formed Metal Framing Solution & Systems Integration: Radius Track Corporation
U.S. Olympic and Paralympic Museum
Design Architect: Diller Scofidio + Renfro
Architect of Record: Anderson Mason Dale Architects
General Contractor: GE Johnson Construction Company
Framing Contractor: Spacecon Specialty Contractors
Facade Contractor: MG McGrath
Cold-formed Metal Framing Solution: Radius Track Corporation