Ceramic Precast Composite Panels
High Performance Structural and Architectural Building Enclosures
Sign in and Register
Create an Account
Overview
Abstract
An innovative lightweight ceramic precast composite panel is introduced in this paper that offers the unique benefits of prefabricated off-site construction. The panel system enables broad application by providing structural strength, thermal efficiency, and a sustainable modular construction solution. Ceramic composite panel technology offers improved public safety over some traditional building systems, and may be an attractive choice for energy-efficient developments. The patented system features excellent fire ratings (ASTM-E119-12) and high thermal insulation values. The thin ceramic concrete shell is lightweight, while still providing structural performance at a significantly high strength to weight ratio. The composite panel provides a high-performance technology at a low-cost due to efficient product manufacturing methods, allowing the technology to be economically competitive with current building systems. In addition, the prefabricated panels can be used as wall, floor, and/or roof assemblies that interface to create a complete enclosure and structural system. The composite building system is designed to meet and exceed the requirements set forth by the International Building Codes. This paper introduces the system, reviews laboratory test results, and presents two projects recently completed in central North Carolina. In these case studies, the ceramic precast panels were successfully implemented after the technology was selected by the architect, reviewed by a 3rdparty engineer who developed engineered shop drawings, and was approved for construction by local city building officials and the North Carolina Department of Insurance.
Authors
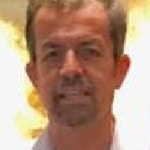
Edward Rubio
American Craftsmen Inc.
er@americancraftsmeninc.com
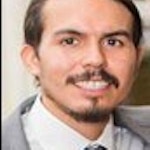
Edward J. Rubio
American Craftsmen Inc.
ejr@americancraftsmeninc.com
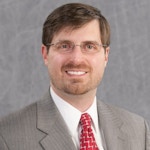
Gregory Lucier, Ph.D.
North Carolina State University
gwlucier@ncsu.edu
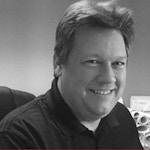
Brian Moskow, PE
Red Engineering and Design
bmoskow@redengineering.com
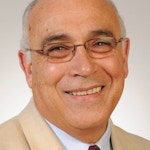
Sami H. Rizkalla, Ph.D., FACI, FASCE, FEIC, FCSCE, FIIFC, FPCI
North Carolina State University
sami_rizkalla@ncsu.edu
Keywords
Introduction
The construction industry faces challenges attributed to building methods, safety both during construction and during occupancy, energy consumption, fire resistance, and costs. Out-dated building methods continue to persist in the
Access Restricted
Background
The proposed system is shown in cross-section in Figure 1. The system consists of conventional cold-rolled steel framing (studs and track, track not shown) encapsulated in a sheet of rigid
Access Restricted
Method
The design and production process for the panels is outlined in this section. Design of the panelized structure and of the panel assemblies themselves is completed with custom-tailored BIM software
Access Restricted
Laboratory Tests and Data
A series of tests have been completed on typical panels, including structural tests at North Carolina State University in Raleigh, North Carolina, where flexural, racking, and concentrated load tests were
Access Restricted
Case Studies
Two case studies are presented in the following sections. Both projects were recently completed in the Raleigh-Durham, North Carolina area.
Hilton Garden Inn
One of the earliest field applications of the ceramic
Access Restricted
Conclusion and Future Work
An innovative prefabricated panel system has been develop and was presented here. The practicality and feasibility of this system was demonstrated through laboratory testing and successfully completed field projects. The
Access Restricted
Acknowledgements
The authors would like to thank American Craftsmen, Inc. of Raleigh, North Carolina for sponsoring the tests presented here. In addition, the authors would like to acknowledge Ted Van Dyk, AIA and his team at New City Design Group in Raleigh, North Carolina for their work on the Mao Residence along with officials from the City of Raleigh and the North Carolina Department of Insurance. Finally, many thanks are due to Khi David Mao for his continued support of this innovative technology.
Rights and Permissions
ASTM Standard E119-16a, 2016, "Standard Test Methods for Fire Tests of Building Construction and Materials," ASTM International, West Conshohocken, PA.
Rubio, Edward. Concrete Composite Wall Panel. U.S. Patent 7,681,368 B1. Filed August 21, 2007, and issued March 23, 2010.
Report 15-5699. Fire Exposure Test on ACI Smartwall System: Evaluation of 3 Hours Fire Endurance. Fenestration Testing Laboratory, Medley, FL. 4/13/2015.
Lucier, G., “Concentrated Load Tests on American Craftsmen Patented Smartwall Panel”, Technical Report IS-11-14, submitted to American Craftsmen by the North Carolina State University Department of Civil, Construction, and Environmental Engineering, Constructed Facilities Laboratory (CFL), Raleigh, North Carolina, August, 2011.
Lucier, G., “Racking Shear Test of Smartwall Panel”, Technical Report IS-10-18, submitted to American Craftsmen, Inc. by the North Carolina State University Department of Civil, Construction, and Environmental Engineering, Constructed Facilities Laboratory (CFL), Raleigh, North Carolina, December, 2010.
Lucier, G., “Flexure Testing of Smartwall Panel”, Technical Report IS-10-16, submitted to American Craftsmen, Inc. by the North Carolina State University Department of Civil, Construction, and Environmental Engineering, Constructed Facilities Laboratory (CFL), Raleigh, North Carolina, November, 2010.